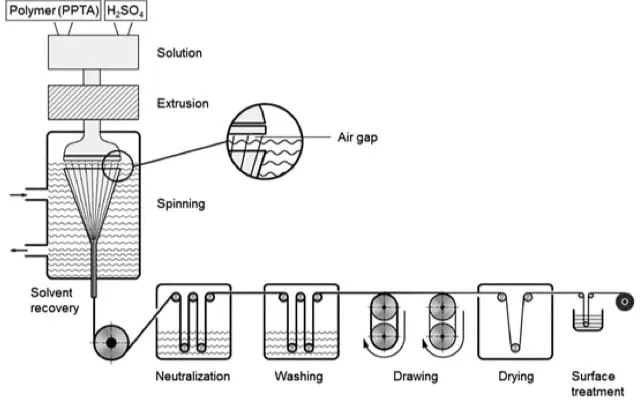
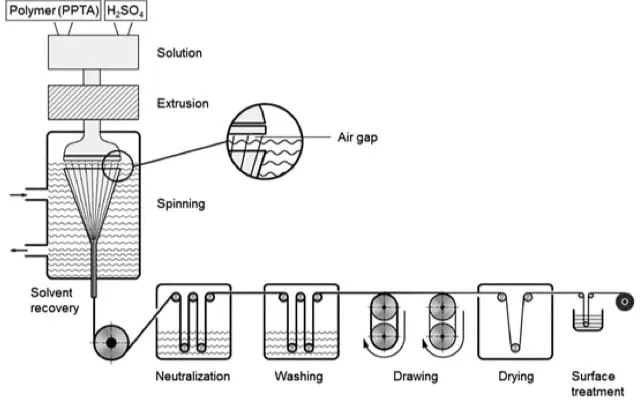
Aramid chemical composition and manufacturing process
Soft-body Armor Analysis and Design for Law Enforcement Officer (Part 2)
This article is part 2 of my portfolio specifically about the Kevlar and the material science behind such soft-body armor.
Read Part 1: Soft-body Armor Analysis
Defects & Strengthening Mechanism#
What make PPTA stands out is not only its intrinsic characteristics but also the way it was treated in post-solute process.
Point defect#
Isolated Chain Ends#
The chain-end defect occurs with mostly at end groups like –COOH, –NH 2 and its distribution are directly affecting deformation, failure process and the strength of PPTA . That is because the water in presence of creates PPTA chain scission by hydrolysis in the solidification process of solution. Also, the treatment to control the defect is using 100% concentration as proposed in Manufacture Process - Step 3.
Interstitial#
The swelling induced by the hydration of Sodium Sulfate () creates interstitial defects. The treatment to control the defect is further dissolute the by prolong the exposure time of fiber to boiling water as proposed in Manufacture Process - Step 7.
Material Treatment#
Surface Heating#
The Young’s modulus determines the extensibility of fiber when deform elastically and partially depends on the molecular orientation angle which can be improved with post-treatment. The heat treatment solely focusing on treating the mis-orientation of PPTA chains with respect to fiber axis and results in a reduction from 12° to about 9°.
Consequently, the increase in total orientation results in increment of the fiber Young’s modulus, hence the elastic deformation ability and the chain linearity which essentially are the determinant of the tensile strength and are the two most important specifications of aramid fiber. More in Manufacture Process - Step 9.
Introduce Epoxy resin matrix#
An adhesive Epoxy resin (E.g. Epon 828) was chosen for joining Kevlar fibers together, increase the attraction force, stiffness and thus strengthening the composite . Specifically, the resin through cross-linking reaction binds the PPTA filaments together and then changes state from a liquid to a solid.
Also, the process of introduce Kevlar into Epoxy resin matrix is via the exothermic reaction which indicates releasing heat involvement and since Epoxy is a thermosetting resin, it will remain formed and cannot be reversed afterwards. More in Manufacture Process - Step 5.
Manufacturing Process#
Polymer Synthesis#
PPTA synthesis process consists of solid state polymerization under dry nitrogen conditions at low temperature in range of 10° - 20° C with N-methyl-2-pyrrolidone (NMP) as the solvent and calcium chloride (CaCl 2 ) as the ionic component
- Step 1: The condensation reaction of para-phenylenediamine PPD () and terephthaloyl chloride TCL () yielding hydrochloric acid (HCL) as a byproduct and results in monomer units.
Solution Polymerization of PPTA
- Step 2: The resulting PPTA polymers then neutralized with dilute Sodium Hydroxide (NaOH) in order to remove Hydrochloride acid (HCL) formed during the process.
At this stage, PPTA chains reportedly has average molecular weight of approx. 48350 g/mol which means it has the polymerization degree of approx. 240 (i.e. has ≈ 240 units in total).
The PPTA chain is fully extended and consists of an alternation of rigid aromatic and amide groups in rod-like form as thermoset plastic with cross-linking and branched chains.
Chain behavior at different stages
In addition, the behavior changes as PPTA dissolved in higher concentration during the Dope Preparation and consists of short range order with long range order in small volume (typical behavior of Liquid Crystalline as discussed earlier). Alternately spun into fully extended chains in Spinning Process.
Dope Preparation#
In order to prepare liquid crystal dopes for the spinning process:
-
Step 3: Synthesized PPTA is dissolved in 100% concentration Sulfuric Acid () in order to achieve low viscosities and anisotropic feature of the spinning solution.
-
Step 4: The dopes that will be used to spin into fibers are melt above the melting point of 80° C.
Spinning Process#
The spinning process of PPTA fibers, dry jet-wet spinning, give higher strength, a higher modulus but a lower elongation :
-
Step 5: The PPTA fibers are extruded in the form of liquid-crystalline dopes at about 85°C via a spinneret at 0.1-6m/s through the spinning nozzle and an air gap about 5mm between spinneret face inside a 1°C Water Coagulation Bath
-
Step 6: The spun yarns then pulled down by the downward stream of the spinning bath at rate of 100-200 m/min
Schematic Production of Aramid Fiber
-
Step 7: The recovered yarns then neutralized with Sodium Hydroxide (NaOH) again and subsequently washing out the water-soluble Sodium Sulfate () with boiling water to remove the introduced _interstitial defects.
-
Step 8: The yarns were draw and dried under tension on roller at the temperature range of 65-130°C at which stage it is the equivalent yarn to Kevlar 29 yarn for ballistic application based on DuPont™ manufacturing
-
Step 9: The surface treatment by apply temperature in range of 250 to 550 °C under 5-50% tension for time less than 10 minutes.
Epoxy Fabrication#
The Aramid/epoxy composites consists of these processes:
-
Step 10: PPTA filaments passed through a mixed solution of diglycidyl-type resin (Epon 828) and 4,4’-diaminodiphenylmethane (DDM) with acetone at a 4:1:4.8 weight ratio.
-
Step 11: The treated fabrics are then dried at 25°C for 30 minutes and then at 70°C for 20 minutes.
-
Step 12: The fiber-reinforced epoxy composites are then cured under ambient conditions for 2 hours at 80°C followed by 2 hours at 150°C at a pressure of 150 psi under heating rate of 3°C/min.
-
Step 13: The molding cavity is then cooled to room temperature and releasing the pressure.
Testing & Quality Control#
According to the primary manufacturer (DuPont™) of Kevlar, the ballistic testing standard for specified soft-body armor is the NIJ standard of the US DOJ. That is, the armor should be tough enough to withstand rounds fired of different types of bullets ranging from 9mm to .44 Magnums (Type II as mentioned in Requirements for soft-body armor).
Specifically, by using a destructive test and measure the indentation depth which is defined as Backface signature (BFS), the NIJ has conducted that that the soft-body armor Kevlar 956 (Kevlar 29) protects against:
-
9 mm Full Metal Jacketed Round Nose (FMJ RN) bullets, with nominal masses of 8.0 g impacting at a minimum velocity of 358 m/s
-
357 Magnum Jacketed Soft Point (JSP) bullets, with nominal masses of 10.2 g impacting at a minimum velocity of 427 m/s
Environmental Impact#
- Impact
Aramid Fiber is technically still a thermoset polymer which is very hard to deal when it comes to disposable. Since it does not melt but decompose at a very high temperature, it creates both human health and environmental health hazard whether its cancerous radiation or toxic gases. Other infamous solutions are burying either under mainland which leaking chemicals into ground water or create plastic island in the ocean which then eaten by sea creature and ultimately taken by human afterwards.
- Proposed solution
Recycle: As mentioned, this is not the primary solution because there is still no definitive solution to recycle Kevlar or even plastic.
Reuse: One way to reuse the body-armor is through thermal degradation in which include the process of pyrolysis and then separate the fiber and resin composite by mechanical washing machine.
The method resulted yarns show 80% decrease in impact resistance, despite that, it still can be managed to reuse in other sectors such as research or teaching purposes.
Processing: Plastic-eating microbes are only on research scale but it has showed promising for plastic disposal.
However, as the bacteria grow stronger, it would require a better immune system to prevent undesired evolution which could end up potentially lethal for human.
- Future Plan
Improvement: Embedding a network of cross-linking carbon nanotubes (CNTs) to decrease the thickness and increase twice the strength of Kevlar .
Concern: The main concern for soft-body armor of researchers is further improving the physical properties of Kevlar fiber through the manufacturing process to maximize the adequacy for special parts like armpit, groin protection.